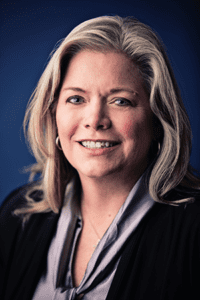
Wichita, Kansas, is best known for being a center of aviation manufacturing. The city, which refers to itself as the “Air Capital of the World,” is home to multiple major aircraft companies and industry suppliers, including Textron Aviation, Spirit AeroSystems Holdings and Airbus Americas Engineering. But what the city is increasingly short of is talent to work at these companies.
“It’s a constant struggle for Wichita,” said Sheree Utash, president of Wichita State University Tech. “There are a lot of job openings and not enough talent. We need a bigger pipeline to fill these jobs.”
It’s an ongoing problem that city leaders have attempted to address through high school training programs, internship opportunities and scholarships to local students. But none of these programs have made a big enough impact.
Last May, Utash was talking with members of the Wichita Community Foundation, which helps people manage charitable giving, and they came up with an idea. Instead of just offering scholarships, what if the city paid all of the relocation, academic and living expenses for students to come to Wichita and complete an Aviation certification training program — then helped them find jobs? “It was a Saturday morning ‘write it on a napkin’ kind of idea, but it ended up having legs,” Utash said.
Foundation leaders thought it was an innovative approach to addressing one of the challenges outlined in its Chung Report, a deep dive study of Wichita’s economic development needs, created by James Chung, a former Wichita resident and current head of Reach Advisors, a New York-based strategy and research firm. The report identified the lack of human capital and training for advanced manufacturing as major obstacles to the city’s economic growth, said Shelly Prichard, president and CEO of the foundation. Her organization had earmarked $1 million to support talent development, so when she heard Utash’s idea she was immediately on board. “We need more people here to keep up with demand, and this was a way to get people to come,” Prichard said.
All Expenses Paid
By July, the foundation committed the first $500,000 to Wichita Promise MOVE with plans to invest more if the program takes off. “It was the largest grant the foundation has ever made,” Utash said.
The core goal of WPM is to remove all the barriers that keep people from getting training to start a new career. “It’s not enough just to give them a scholarship,” Prichard pointed out. People need to live, eat and support their families, and they can’t do that if they have to quit their jobs to go to school full-time. “Wichita Promise MOVE removes those barriers.”
The program covers relocation costs, housing, food and transportation along with tuition and fees for students to complete one of two WSU Tech certification programs, in sheet metal assembly or process mechanics. The training lasts six to eight weeks.
To be eligible, students must reside at least 75 miles outside of Wichita and pass basic enrollment criteria, including a math assessment and a drug test. Once they complete the training, they are guaranteed an interview with at least one local aviation company, with the potential for a sign-on bonus.
Finding Candidates
WSU Tech is using the money to cover all of the students’ costs and to support a national marketing campaign via traditional and social media channels. It is the first national marketing effort WSU Tech has ever undertaken, and it was a steep learning curve, Utash said. But the initial response has been promising. Utash’s initial goal was to find 50 candidates to put through the program by the end of 2018, and they were close to meeting that target at the time this article was written.
Since launching the campaign, they’ve had more than 1,000 inquiries from every state in the nation, and 91 people started the application process. Twelve students were selected for the first cohort, and 31 were being considered for the second program, which began in October. Several students from the first group were offered jobs before they even began the training, based on their initial screenings. “Local companies are fighting to hire these students,” said James Hall, dean of aviation technologies at WSU Tech. “They are very excited about the program.”
The students in the first two cohorts range in age from late teens to mid-30s, with varying education and work experience. “They don’t need to have prior experience in manufacturing to be eligible, but we included the math test because math skills have been a barrier in the past,” Hall said.
The instruction focuses on knowledge accumulation and practice. While the training is only six to eight weeks, it is full-time, Hall noted. “Our students are with us eight hours a day, five days a week, just like a traditional work environment. Over the course of six weeks, that translates to 240 hours in class, plus homework and online assignments.
The sheet metal program was already part of WSU Tech’s curriculum, though Dean’s team adapted it to be shorter and more intensive, so the students could be ready to work sooner. The process mechanics course was developed specifically for the WPM program.
In both cases, WSU Tech faculty worked with industry leaders to understand the knowledge and skills they want these candidates to have and the kinds of projects they will be working on. “Industry feedback helped to shape a lot of the curriculum,” Hall said. The faculty are also open to tweaking the program as industry needs evolve. For example, Spirit AeroSystems is currently building a very large structure for Boeing, so they asked that students practice with larger fasteners. Instructors also implemented a new device provided by the company to time how fast students can complete certain tasks.
A Helping Hand
Industry involvement doesn’t end in the classroom. Business owners throughout Wichita are getting involved by pitching in to host student dinners and offering deals on hotels and transportation. One real estate company even donated $80,000 worth of furnished apartments for students to use while they are training to help stretch the grant further, Prichard said. “The whole community wants it to be successful.”
To further ensure the students stay on track, the school has hired a success coach to work with them every step of the way. “It’s like career counseling on steroids,” Utash said. The coach makes sure they get settled into their new homes, encourages them to at-tend weekly student dinners, and checks up on them regularly to make sure they are attending classes and finding their way around the city. She also gets involved if they start to fall behind. In one case, the coach followed up with two students who failed to sign up for an online occupational safety course after checking in with their professor. In another, she stepped in to comfort a student who was scared and homesick after arriving “She has added a human touch to this process to make sure every student is successful,” Utash said.
It’s Not a Job, it’s a Career
Assuming students complete the program and land jobs, they can expect starting salaries of $13 to $15 per hour with raises every 90 days, getting to about $20 an hour within a year, Hall said. “That is a livable salary in Wichita.”
Utash doesn’t see that as the end goal, however. “It’s a first step for these kids to build a career in aviation,” she said. If they stay in the industry they will have opportunities for promotion, and many companies offer tuition reimbursement programs, allowing students to build on the initial certification toward an associates or bachelor’s degree. “Some kids have a hard time figuring out how to get started,” she said. “This program gets them there.”
Prichard is equally optimistic about WPM’s success and hopes the foundation will find additional donors to keep it going beyond the initial investments. “It’s a feel-good program for students, with absolute economic benefits,” she said. And while the model may be unusual, it appears to be solving a significant talent need in the community. “I hope we’ve shown people that this can work and they should want to be a part of it.”
She believes this model could be replicated in other communities — if industry, academia and community foundations work together toward common goals. “You have to find people you can trust and who are willing to experiment with new ideas,” she said. While there are no guarantees that this program will pay off for Wichita or any other city, it has the potential to change lives while delivering a positive economic impact, she said. “That makes it worth taking the risk.”